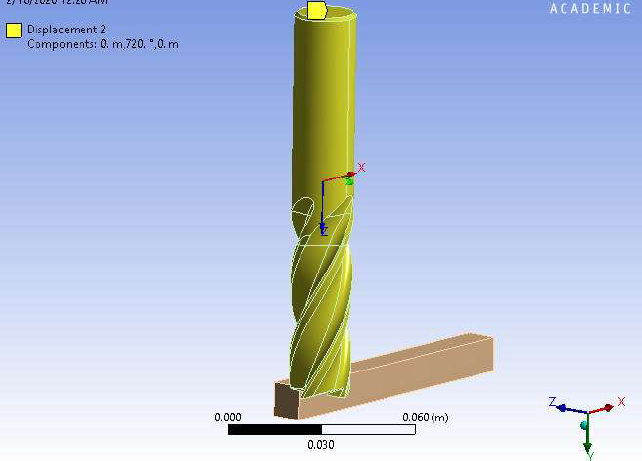
Optimizing the Performance of Structural Steel End Milling Cutters in Machining Aluminum Alloy Workpieces: A Finite Element Method and Surface Optimization Approach
The milling machine stands as a versatile and indispensable conventional tool, exhibiting a broad spectrum of metal cutting capabilities. Its proficiency extends to intricate operations such as indexing, gang milling, and straddle milling. This study aims to forecast the optimal Angular Displacement of the Structural Steel Milling Cutter and the optimum feed for the Aluminum Alloy workpiece by leveraging the surface optimization tool within ANSYS 19.R3.
The comprehensive examination of the Surface Optimization tool’s outcomes underscores its superior efficacy compared to the Finite Element Method (FEM) tool. This scrutiny establishes the dominance of the Surface Optimization tool in predicting high-performance results. Furthermore, the exploration delves into the creation of a mathematical model for the End Milling Cutter. The ensuing 3D model, crafted using CATIA 5.1, facilitates simulation through Finite Element Analysis. The primary objective is to ascertain the optimal Angular Displacement of the Structural Steel Milling Cutter and the ideal feed for the Aluminum Alloy workpiece.
In this pursuit, the model considers specific tool geometry, minimizing the repercussions of Equivalent Stress, Equivalent Elastic Strain, and Total Deformation on the End Milling Cutter induced by cutting forces. The simulation tool of choice is the Response Surface Optimization tool embedded in ANSYS 19.R3, underscoring the commitment to precision and advanced analytical methodologies in this research endeavor.