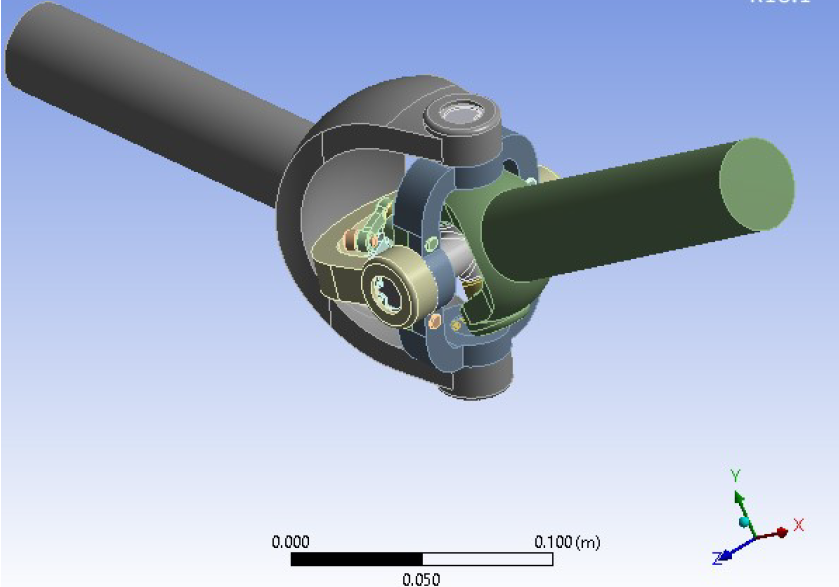
Finite Element Method (FEM) Performance Analysis and Advancements in the Development of the Thompson Constant Velocity Joint
The Thompson Constant Velocity Joints play a pivotal role in maintaining constant velocity power transmission between driving and driven shafts, facilitating both power transmission and shaft flexibility. This mechanism involves a pair of shafts connected through a transverse axis, typically oriented at a 90° angle to each other. Notably, the Thompson Joint eliminates the need for intricate gearing devices to rectify misalignment, thus optimizing torque transmission efficiency.
Despite its efficacy, the Thompson Joint encounters challenges related to design errors, assembly discrepancies, material deficiencies, maintenance lapses, material transformation failures, cyclic loading-induced angular displacement, wear, and noise. Of particular concern is the occurrence of shear failure during operational conditions.
The central goal of this study is to address and diminish shear failure in the Thompson Joint. The current design and modeling of the joint are meticulously executed using CATIA software, followed by a comprehensive analysis conducted through the robust ANSYS software. To enhance performance, a proposed modification focuses on optimizing the pin design. This refined Thompson Joint iteration is meticulously modeled using CATIA, and both static and dynamic analyses are rigorously carried out using the ANSYS software suite.
Upon comparing the original design with the modified/proposed design, a discernible reduction in equivalent stress is observed. This reduction stands as a testament to the efficacy of the proposed design in ameliorating shear failure, thereby augmenting the operational robustness of the Thompson Joint. This study underscores the intricacies of joint design, coupled with advanced modeling and simulation techniques, in enhancing the reliability of critical mechanical components.